Is the website displaying in the correct language? Please confirm or select a different language.
Your region has been set automatically. Please confirm or select a different region.

1280 in Full Control
Dual 1280 Enterprise Series weight indicators and a 920i controller drive a masonry plant’s automated processes in Mexico.
In the industrial outskirts near Mexico City, a newly-constructed cement and mortar manufacturing plant utilizes a unique solution to automate the facility’s operations. Rather than implementing industrial computers to manage its complex processes, Rice Lake’s programmable weight controllers run the show.
Publish Date: 03/28/2019
Controlling Weight and Batching Processes with Rice Lake Scale Indicators
Although Mexico may be widely known for warm weather, delicious fruit and picturesque beaches, it has another side to offer. The country’s industrial economy is quickly rising to transform its global identity. The heart of this industrial growth can be found in construction, where masonry products play a vital role.
To elevate quality, ensure consistency and reduce costs, automation is key to the successful manufacture of bulk construction materials. At the batch plant, each step of the process is under Rice Lake controllers’ intelligent and robust control. It begins with a series of outdoor conveyors that transport raw materials, such as sedimentary rocks and chemical compounds, into the facility.
Next, massive ovens heat these materials to temperatures in excess of 2,500° Fahrenheit (1,371° Celsius). The process transforms the components into calcium silicates, aluminate and aluminoferrite, which then move down the line into dryers. After all moisture has been removed, a precise mix is required. Automated mixers combine ingredients using weight from Rice Lake load cells, then pass the final product to the bagging line.
Here, empty bags are positioned on a filling tube and held in place by robotic clamps. Scales monitor weight, communicating back to the control room in real-time. When 80 pounds (36 kilograms) is reached, the feed is paused, and the bag is sealed, released and transported on conveyors to the shipping warehouse.
The entire process may seem simple enough at first glance; however, at the center of this smooth-running operation is the 1280 indicator's powerful hardware and sophisticated custom programming. Scale dealer Acemex-Electroamerica completed the impressive project, including the installation of six scales as well as programming two 1280 indicators and one 920i indicator.
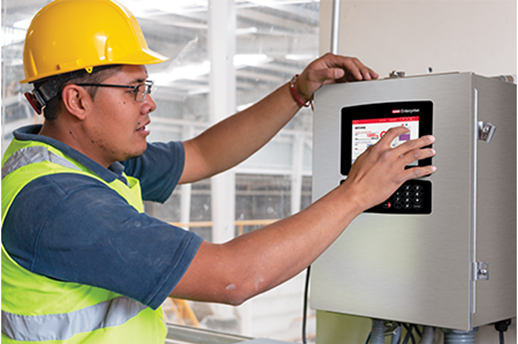
The 1280 programmable indicators’ screens were customized by scale dealer Acemex-Electroamerica to display process status and offer manual control over alarms, control valves and engines.
Automating Mortar with a 1280 Digital Weight Indicator
One 1280 programmable indicator is dedicated to the grey mortar process. Three scales are connected, each of which can be monitored for live weight readings. In each of the four large sand hoppers adjacent to the building, a sensor is installed which communicates with the 1280 indicator. When product is present, the 1280 indicator presents a visual representation, and the operator knows to press the on-screen Start key. Each stage can also be controlled manually by touching the 1280 indicator’s screen. Sensors are present in the plant’s three engines (and throughout the system) to show when equipment is running.
A sensor sends an exact reading to the 1280 indicator during the heating and drying phase to display a temperature value on the 1280 indicator’s main screen. The oven and dryer can be started automatically or by pressing another custom key on the indicator’s touchscreen.
Custom Formulas and Screens with the 1280 Digital Weight Indicator
With the 1280 indicator, a nearly infinite amount of formulas can be stored. A custom formula configuration screen lists all ingredients and displays them in the order they will be processed. If changes to the formula are necessary, the operator can simply swap materials with another stored in the system and/or reorder the sequence in a matter of seconds. The desired weight of each ingredient is also shown on the screen and can be edited to fine-tune the finished product or create an entirely new result.
Timers for each stage are also displayed on the screen of the 1280 indicator. Multiple timers can be adjusted as needed until the process is perfected. All configuration is password-protected to ensure safety, and full control of the system is available to start/stop at any time through the “Manual” screen. On this screen, each controllable function is listed and can be turned on or off, including audible alarms, control valves and engines located throughout the facility.
Doubling Efforts with a Second 1280 Digital Weight Indicator
The second 1280 indicator controls the sand receiving and white mortar process, and is set up similar to its nearby twin. Its main screen begins an automatic formula, and each of the system’s controls can be operated manually. Hopper widgets show visual representations of current fill levels, and just like the first 1280 indicator, valves and engines are controlled and three connected scales’ weight readings are displayed.
Finishing the Process with a 920i Digital Weight Indicator and LaserLight Remote Scale Displays
The 920i indicator is in charge of the bagging process. Four scales are installed in this area, two on each side of the back-to-back bagging systems. Four LaserLight® remote displays brightly show the weight reading of each scale as bags are filled.
Custom Scale Software from Acemex Authorized Scale Distributor
Completing the system is WeighWorks ®, Acemex’s custom PC software. Within this application, a vast amount of information is readily available. This includes product information, lot numbers, batch and product data, supplier and driver IDs, reports and much more. Gross weight can be analyzed from any scale in the system and custom tickets can be created or printed at any time. The operator simply specifies the batch and product to dive into the data.
Material, supply and production information can be generated into summary documents and exported as Excel ® files, .TXT or .PDFs. Everything is 100 percent customizable and filterable by date, time, product or scale number.
All of this is performed without a traditional PLC and would not have been possible without the 1280 programmable indicator’s power and limitless customization, as well as Acemex’s programming expertise. Jessica Rosete, systems engineer for Acemex, and Gonzalo Aceves, the company’s director and CEO, programmed and installed the system, demonstrating the capabilities of Rice Lake’s skilled dealers and high-tech equipment.
The fully automated batch material processing system is one of the most advanced control applications to date. All signs point to a future filled with enormous growth for Mexico’s industrial economy, and Acemex-Electroamerica is helping build this future with Rice Lake’s programmable weight indicators and controllers.
Featured Rice Lake Products
Subscribe to Rice Lake Magazine
Sign in or create a Rice Lake website account to request a Rice Lake Magazine filled with application stories like this one be sent to you.
Account Sign In Create an Account