Is the website displaying in the correct language? Please confirm or select a different language.
Your region has been set automatically. Please confirm or select a different region.
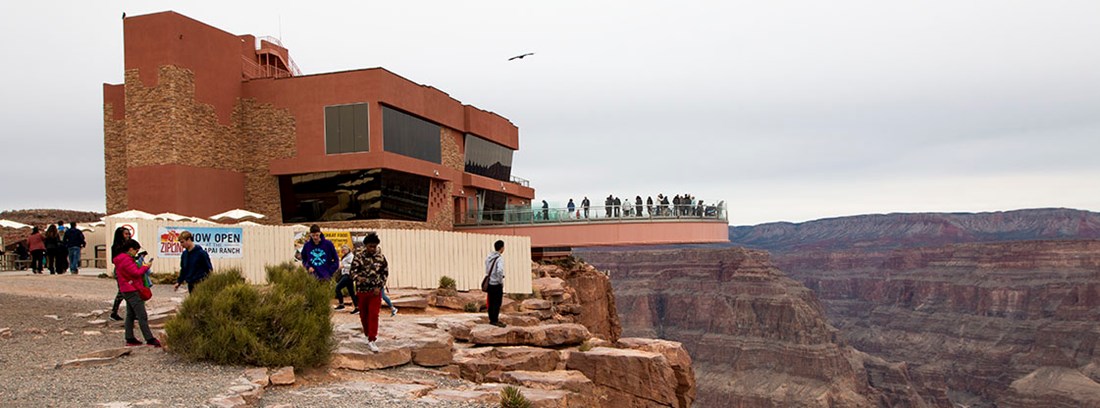
A Spark of Innovation in the Grand Canyon
In rural Arizona, a reliable mix portable batching system powered by Rice Lake’s CB-3 concrete batch controller upgraded the visitor center for the stunning Grand Canyon Skywalk.
Deep in the Arizona desert lies the Grand Canyon Skywalk, a 10-foot-wide, horseshoe-shaped glass bridge that extends 70 feet from the edge of the Canyon. Constructed from 2004 to 2007, the Skywalk is strong enough to bear the weight of more than 70 passenger jets. It’s an impressive and necessary feat, considering nearly one million thrill-seeking guests visit Grand Canyon West every year—and a Rice Lake CB-3 concrete batch controller is helping build a new visitor center.
Grand Canyon West is owned and operated by the Hualapai Indian Tribe. At Grand Canyon West, guests can explore a variety of outdoor recreation opportunities, such as hiking and river and aerial tours. The West Rim that hosts the Skywalk is a desert splashed with color, while the South Rim is the center of a dense forest. As you might expect, you’ll hardly find a shortage of things to do at the Grand Canyon.
But until recently, the Skywalk visitor center and parking lot were growing overcrowded. With an ever-increasing amount of foot traffic flocking to the Skywalk every year, more space for guests was no longer optional. An upgrade was necessary.
Jarom Hatch was one of the contractors hired to revamp the Skywalk’s visitor center and parking lot. Though initially in the pre-cast business, in 2016 Hatch decided his company, Hatch Industries, would bring part of the supply chain in-house by producing its own ready mix.
With a location as rural as the Grand Canyon Skywalk—an hour away from the nearest town—and highly perishable concrete, Hatch had the perfect tool for the job.
Rice Lake’s CB-3 concrete batch controller, paired with the Reliable Mix RMX 100 Portable Batch plant, allowed for batching directly on the construction site.
The CB-3 serves as the “brains” of the weight-based batching operation, allowing the batch operators to enter a mix design and load quantity; from there, the CB-3 performs automated batching and produces a consistent result every time.

With a portable batch plant and the CB-3, concrete can be batched onsite, preserving product and conserving equipment, namely trucks. This decreased overhead costs and ensured every batch of concrete was put to use. The latter can be difficult due to the volatile nature of concrete. As soon as water is added, the hydration process begins and concrete starts to harden; concrete has to meet strict specifications, which becomes less likely after more than 90 minutes in the mixer.
Complementing its portability, this type of batching system is beneficial from an economic standpoint. Portable systems allow users to produce ready-mix anywhere in the country, and as a result, follow the economy. Onsite batching with the CB-3 also means less running of the mix truck, which helps keep overhead costs down. With all of these advantages, it’s no wonder why the CB-3 portable batching system was the best choice for the Grand Canyon Skywalk’s renovation.
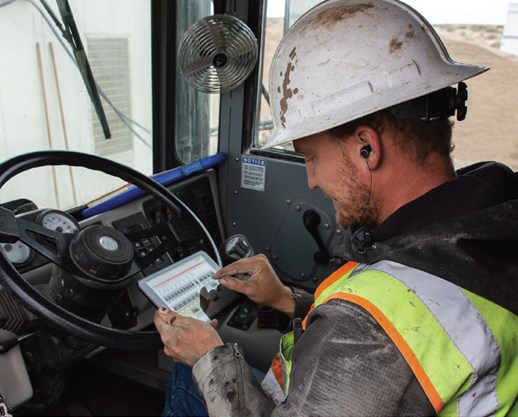
The flexibility of the CB-3 doesn’t stop there. With remote batching capability, CB-3 users can access the system from a cell phone or tablet.
“We know how much is in our silos and our bins at all times,” Hatch said. “It makes it much easier to operate, especially at a high capacity.” Traditional controllers require the press of a physical button to initiate the batching process. However, thanks to the CB-3’s ability to batch remotely, users no longer have to physically go to a workstation to monitor batching. Operators don’t have to leave the truck to queue and start a batch, maximizing efficiency in a time-sensitive operation.
With consistency so vital to the ready-mix business, it’s no wonder that in addition to time, weight is an important component of concrete batching. Mix designs need to be accurate and repeatable, particularly for government jobs. According to Hatch, the CB-3 concrete batch controller has helped batch operators at Hatch Industries achieve 0.5% accuracy. “In a 19,000-pound batch of rock, it’ll get within 10 pounds of the mix design, which is incredible,” Hatch said. Accurate batching helps operators get the most value out of their plant. If a batch strays too far from its intended specifications, it is rejected, a costly and wasteful outcome of a lot of hard work. The CB-3 proved a valuable tool for getting the most out of each batch of concrete.
The CB-3, combined with the Reliable Mix RMX 100 Portable Batch plant, proved a revolutionary system for Hatch. It was the first of its kind, so the experts at Rice Lake kept in touch, eager to hear about its performance.
When the system needed a repair, a Rice Lake service technician traveled to Hatch’s site on a weekend to get it back up and running. This meant a lot to him. “They worked all weekend so we wouldn’t be shut down on the weekdays,” he said.
With the help of the CB-3, Hatch was able to improve Grand Canyon West’s visitor center and parking lot. Batch operators were able to take advantage of the plant’s portability, keeping the concrete from expiring and fulfilling their commitment to the Hualapai tribe.
“It was beyond what I imagined,” Hatch said. “As my business grows, the CB-3 is going to be able to keep up with it.”
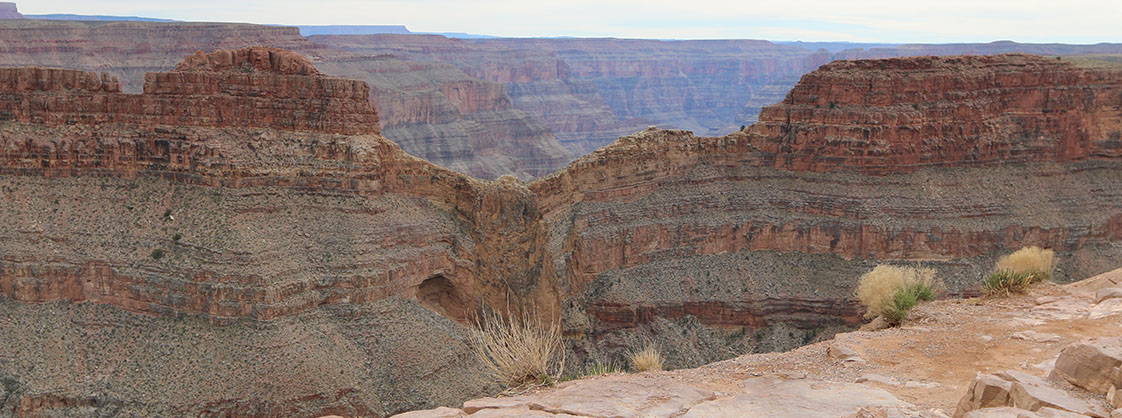
Subscribe to Rice Lake Magazine
Sign in or create a Rice Lake website account to request a Rice Lake Magazine filled with application stories like this one be sent to you.
Account Sign In Create an Account