Is the website displaying in the correct language? Please confirm or select a different language.
Your region has been set automatically. Please confirm or select a different region.
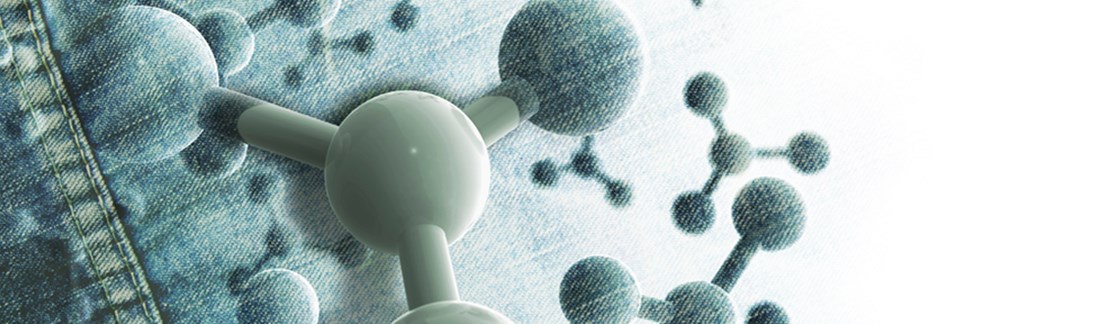
It's Alive!
Publish Date: 12/21/2010
In 1955, the world of blue jeans changed forever. When James Dean donned his iconic denim threads in Rebel without a Cause, pop culture instantly adopted the look. No longer were they referred to as “waist overalls” most commonly worn by painters, mechanics, and old cowboys. Blue jeans became cool, every teenager wanted a pair, and the demand hasn’t let up in the over half-century since. Today, the $700 billion global blue jeans market is so prevalent in America that 12 pairs are sold every second in the U.S., and the average American owns seven pairs. Few things are more identifiable with American culture as blue jeans.
The blue jean has greatly evolved since its popularity skyrocketed. A solid-blue straight-leg soon wasn’t stylish enough. Stone-washed, distressed, and every shade of blue now fill walls of clothing stores, but few know how these styles are achieved.
Initially, special pumice stones were used to customize jean appearance; however, they had major drawbacks. Not only did they weaken the jeans, they also produced inconsistent results and were environmentally unsafe. Special machines had to be used to wash the jeans with the stones. In the late 1980s, the industry developed what is now used today: tiny proteins known as enzymes to “bio-stone” denim. These environmentally friendly chemicals are naturally created by living organisms, which is more economical. They also produce repeatable results and maintain the jeans’ structural integrity. It’s as if James Dean combined forces with Albert Einstein for the benefit of fashion!
IOGEN Corporation is a leader in enzyme research and implementation. They manipulate micro-organisms to produce specific enzymes that facilitate production of a wide variety of products, including ethanol, papers and textiles, and, of course, blue jeans—so, if one drives to a clothing store using ethanol-enhanced gasoline and writes a check for blue jeans, IOGEN can be thanked for making the entire process possible.
But IOGEN’s laboratories in Ottawa, Canada, had a problem. Fiber-digesting enzymes floating around in fermentation chambers are difficult to measure. Quantities are important so enzyme levels can be monitored as they are researched. At first, they used a marker to label the chambers with lines indicating fluid levels, but more precise measurements were desperately needed.
Bogie Ploch, fermentation supervisor at IOGEN, had an idea. His lab has walls full of fermentation chambers: small-scale testing vessels to research enzyme effectiveness. If the fermentation chambers could be effectively weighed, the monitoring process would be far more intuitive. Instead of exercising guesswork to estimate levels between lines, precise weight readings could be used; however, devising a system to work with existing equipment would not be easy—that’s where Rice Lake and GTR Scales came into play.
Jeff Wallace, owner of GTR Scales in Arnprior, west of Ottawa, thrives on custom applications. Not one to shy away from a challenge, he used Rice Lake load cells and instrumentation to customize the container and attach a load cell directly to the vessel—an industry first. This allows data collection to be done quickly and accurately. “Since it’s a sealed unit, nothing could be inserted to measure the level,” Jeff explains. “So we modified the rig itself. We used IQ plus 355 indicators with analog output so it can report back to the PLC, and they have an automated system to collect data.”
IOGEN is very pleased with the custom setup. “Since the manufacturer of the vessels doesn’t provide an option with load cells built in,” Bogie proudly explains, “this unique system gives IOGEN an advantage over our competitors. The indicators are very nice, and GTR did an excellent job. We haven’t had any problems with the indicators or load cells. Monitoring enzyme levels is much more scientific now.”
Initially, only a handful of the over 20 fermentation chambers were customized; however, those have been so successful that the remaining vessels will soon be fitted with load cells as well. Eventually, the entire lab will be accented by the comforting red glow of the IQ plus 355’s LED display: a perfect nightlight for the micro-organisms that make our jeans possible.
Subscribe to Rice Lake Magazine
Sign in or create a Rice Lake website account to request a Rice Lake Magazine filled with application stories like this one be sent to you.
Account Sign In Create an Account