Is the website displaying in the correct language? Please confirm or select a different language.
Your region has been set automatically. Please confirm or select a different region.
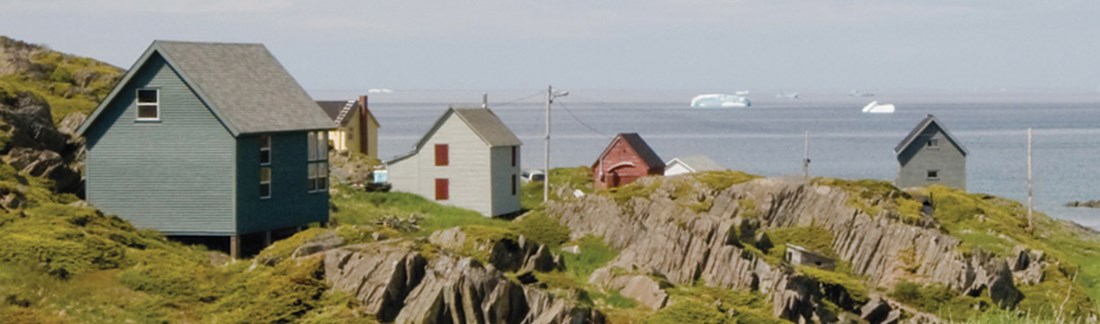
Newfoundland: Where Shrimp, Icebergs, and Moose Roam Free
The 920i® controls an NDS production line where 120,000 pounds of shrimp are processed each day.
Twillingate, NEWFOUNDLAND — Twillingate is a town of 2,448 hardy people located on the causeway-connected Twillingate Islands in Notre Dame Bay off the northeastern shore of the island of Newfoundland. The four-hour drive brings us from the charming city of Saint John’s through forests of increasingly dwarfed pine into tundra-like landscape where moose browse along the roadside between sparse one-story villages. The Twillingate harbor is often populated by mountainous icebergs, giving rise to the local tourist attraction “Iceberg Man Tours” and the town’s title of “Iceberg Capital of the World.”
Our attraction is the Notre Dame Seafood Company (NDS), a very satisfied customer of The Scale Shop Ltd. of Mount Pearl, Newfoundland, founded by Wayne White in 1985. Mick Beswick, scale technician with The Scale Shop Ltd., is taking us to see the application of a 920i® controlling a NDS production line where 120,000 pounds of shrimp are processed each day from late May through September.
Kevin Lambert, NDS maintenance engineer, takes us on a walkabout that requires two full changes of outerwear, hair covers, coats and boots; blue gear for low-risk areas and white for high-risk areas. It takes matured shrimp 20 minutes to go through processing which includes cooking, peeling, washing, mechanical sorting, manual inspection, primary freezing, glazing, grading, bagging and boxing.
Kristi Gay, Rice Lake software engineer, in cooperation with The Scale Shop Ltd., wrote the program that closes the hopper and starts the conveyor in the system’s fill/dump cycle that feeds the large shrimp cooker. This single unit controls the feed rate, and hence the production of this state-of-the-art facility. Before the 920i was installed, the system was time dependent; a batch would be dropped onto the conveyor belt every 25 seconds. With the 920i controller, production rates are keyed into the unit, and the 920i takes over from there, maximizing the throughput of the entire production process.
Kristi makes it sound simple: “Now the operator just keys in the weight-per-hour (how many pounds of shrimp they wish to process per hour), and the time is automatically calculated based on how long it takes to fill the hopper to determine how long it should be held before discharging the shrimp to the conveyor to achieve that target rate.”
According to Wayne White, “It is great to achieve the goals of so many different types of customers and applications with just one instrument. Every user program is different from the next, based on the customers’ needs, whether it is weighing shrimp onto a conveyor, weighing beef in-motion on a hanging scale, or weighing boxes and printing labels. The more information given to my application technician, Mick Beswick, the better the outcome for the customer and end user.”
Mick remembers the phone call that came at 10:00 one night a week after the installation. “I was able to assist Kevin over the phone. The 920i wasn’t seeing zero so the hopper wouldn’t close. After taking Kevin through a simple adjustment of the motion band, I was able to resolve the problem, and production was resumed preventing any major loss of product.”
Kevin Lambert verifies that the outcome has been great for Notre Dame Seafoods. “The beauty of the 920i system is how easy it is to adjust when we need to increase or decrease production due to the grade of shrimp.”
Just before this magazine went to press, The Scale Shop Ltd. received a call from a customer in Labrador who required a replacement system for a shrimp bagging scale which failed, and spares were no longer available. Receiving the call on a Friday, a 920i with a custom program was installed and tested the following Wednesday, much to the great satisfaction of the customer.
Wayne is justly proud, “We provide our customers with first class service support. We pull out all the stops to get our customers back online as soon as possible.”
Subscribe to Rice Lake Magazine
Sign in or create a Rice Lake website account to request a Rice Lake Magazine filled with application stories like this one be sent to you.
Account Sign In Create an Account