Is the website displaying in the correct language? Please confirm or select a different language.
Your region has been set automatically. Please confirm or select a different region.
Operation, Capacity Versus Resolution, and Common Types of Load Cells
An Introduction to Load Cells
A load cell (also called a transducer) converts a mechanical force into an electrical signal. In its simplest form, the load cell is a precision-machined metal element that bends with the force of loading (when weight is applied). In a cavity on the metal element, typically four strain gauges are bonded at points to form resistors, making an electrical circuit called a Wheatstone bridge circuit.
Initially, the four gauges are balanced; if excitation voltage is supplied to the load cell when no load is applied, the output voltage is zero. When a load is applied, the load cell compresses (in a compression-mounted load cell, where the load cell is beneath the weighing vessel or other load-receiving element) or stretches (in a tension-mounted load cell, where the weighing vessel is suspended from the load cell).
The load cell’s compression or stretching causes the metal element to bend and the gauges to become unbalanced, which changes the strain gauge resistance. The Wheatstone bridge circuit amplifies the small resistance change to a usable electrical signal (usually measured in a few millivolts) proportional to the applied load. The load cell transmits this signal via a cable to a controller that converts the signal into a weight measurement.
Depending on the application, a weighing system can include one or more load cells. When an application such as a weigh hopper requires multiple load cells (called multiple load points), each load cell should measure the same proportion of the total load. In a three-load-point system, each load cell should measure exactly one-third of the load, and in a four-load-point system, each should measure exactly one-quarter of the load.
When possible, it’s better to use three rather than four load cells because the three load cells align perfectly in one plane and the hopper’s weight will be perfectly distributed among them. When four or more load cells are used, they must be carefully leveled to ensure that all are on the same plane so that each receives the same load during weighing.
Capacity Versus Resolution
A load cell’s resolution will determine what sensitivity (or readability) it can attain for a given capacity. That is, the resolution of the weighing system (whether it has one or multiple points) equals the system capacity divided by its sensitivity. Simply put, the higher the capacity system, the lower the resolution and sensitivity. Consider for instance a 5,000-pound system divided by 1 pound would be a 1:5000 system. That same 5000-pound scale displaying the weight in 0.5-pound increments would change to 1:10,000 (5,000 pounds divided by 0.5 pounds). Understanding this is important because as a scale’s resolution gets higher, the actual millivolt output per increment gets smaller. The smaller each millivolt reading, the more difficult it is to detect small weight changes. This makes it more difficult for the load cell to deliver accurate weighing results and the digital indicator to display stable readings.
Common Load Cell Types
Common load cell types for weighing applications include S-beam, shear beam, bending beam, canister, rocker and double-ended shear beam.
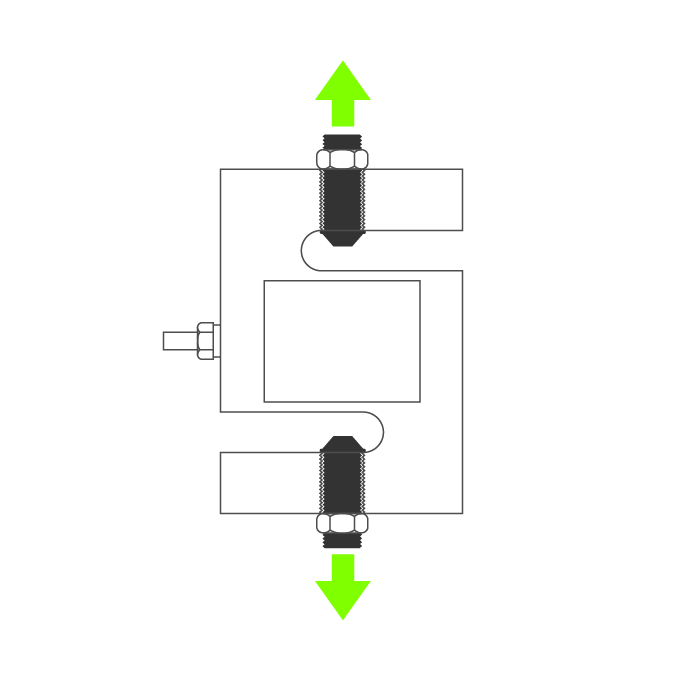
S-Beam Load Cell
An S-beam load cell is shaped like the letter S. This load cell is typically used to hang or suspend a weighing vessel so that the load cell applies tension to (or stretches) the load cell. The load cell capacity of an S-beam typically ranges from 25 to 40,000 pounds.
Shear Beam Load Cell
A shear beam load cell is shaped like a beam and typically supports the weighing system so that the load applies compression to the load cell. A shear point is machined inside the beam to protect the load cell from side loading forces. The shear beam load cell's capacity typically ranges from 1,000 to 50,000 pounds.
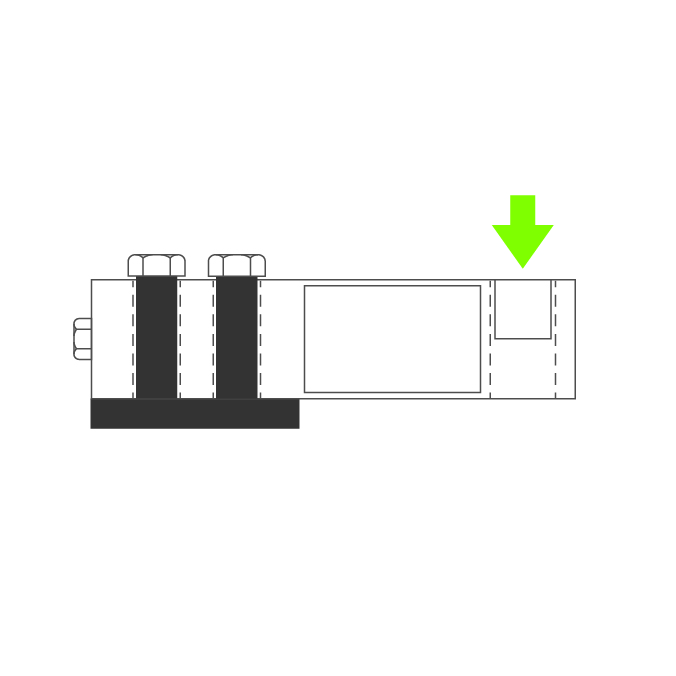
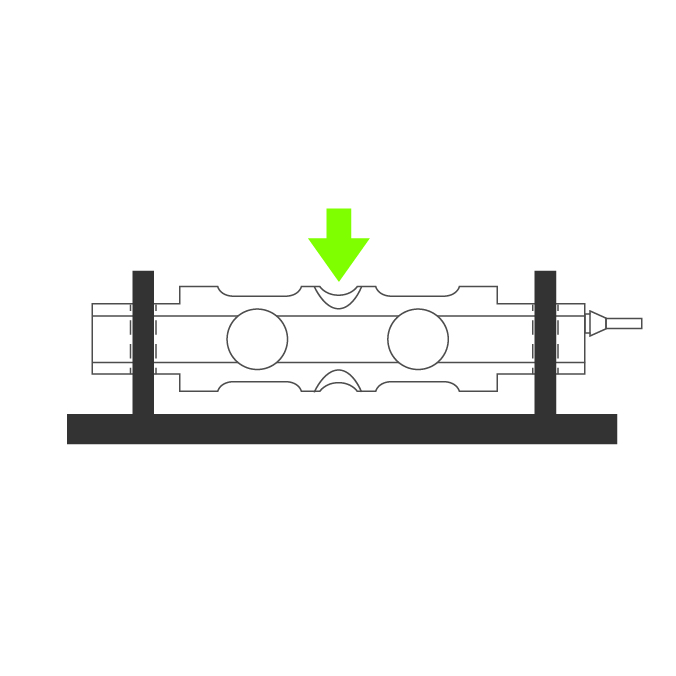
Double-Ended Shear Beam Load Cell
A double-ended shear beam load cell offers a large capacity range - from 1,000 to 2,000 pounds. This compression load cell is configured like two shear-beam load cells positioned end to end and consumes less space than two shear beam load cells would require to achieve the same high capacity. The load cell is also less expensive in high-capacity applications than the canister load cell and doesn't require checking.
Bending Beam Load Cell
A bending beam load cell is another compression load cell and looks similar to a shear beam unit. However, it has a much lower capacity - typically from 50 to 2,000 pounds.
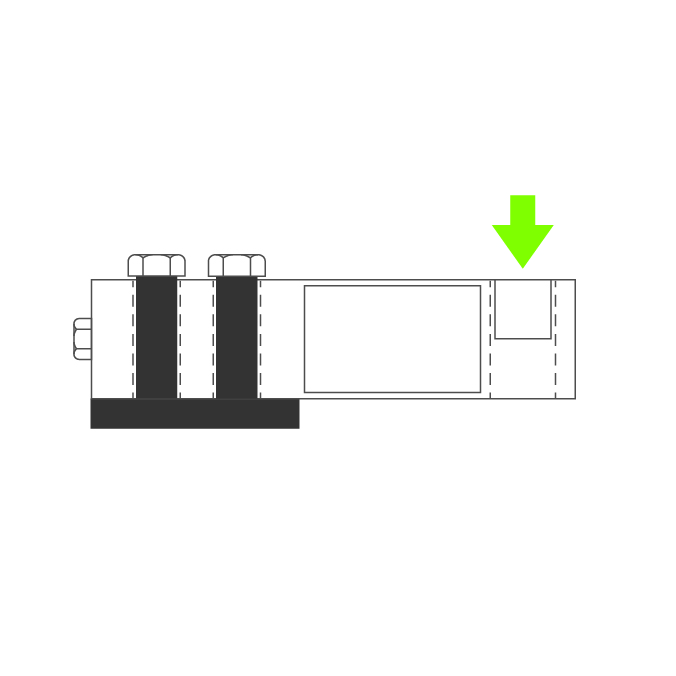

Canister Load Cell
A canister load cell is the oldest load cell type. Also a compression device, it’s shaped like a vertical canister and can handle loads from 100 to 1,000,000 pounds. The canister load cell’s drawbacks include its relatively high cost and the fact that it requires checking (installing check or stay rods to hold the weighing vessel in place on the load cell’s top plate during weighing). For these reasons, about 90 percent of canister load cells on the market today are used to replace older canister load cells on existing weighing systems.