Is the website displaying in the correct language? Please confirm or select a different language.
Your region has been set automatically. Please confirm or select a different region.
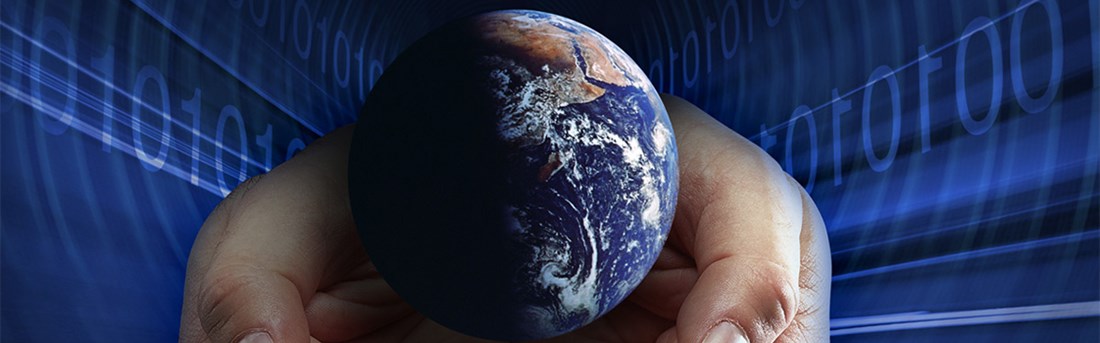
Weighing the World
Rice Lake's products are used throughout the world. Learn about applications in Mexico, Germany, the United Kingdom, Singapore and Ukraine.
International Scales
Mexico
920i® packs tomatoes perfectly
SAN ISIDRO MAZATEPEC, Mexico —
Desert Glory Ltd. is the largest producer of cherry tomatoes in North America. This 400-acre operation controls the entire production starting from seed. They are grown in four-acre greenhouses that are completely enclosed. Rainwater never touches these pampered tomatoes. Desert Glory treats and filters the water and adds fertilizer. The ripe tomatoes are harvested, trucked to the on-site packing plant, washed, graded and immediately packed in mesh bags with the stems still attached to the tomatoes. By leaving the tomatoes attached to their stems, they continue to receive stem nutrients which makes the tomatoes sweeter, but also more difficult to pack efficiently.
At one time, workers packed the tomatoes in mesh bags and placed the bags on a conveyor. At the end of the line, samples of the 12-ounce bags were weighed on a Rice Lake SURVIVOR® CW-80 Checkweigher, and tomatoes were added or removed as needed, which took extra time.
Gustavo Vera, director of total quality management, asked Gerardo Yañez of Basculas Yañez Rios to help streamline the Desert Glory process. Gerardo, who had been providing scale calibration service to Desert Glory, recommended the incorporation of a 920i® HMI programmable indicator/controller into the production line. He developed a system that not only increases through-put, but is also easy for operators to use. It provides real time production and traceability information that Desert Glory needs.
Basically, the 920i system controls 24 checkweighing scales.
Each production line has an enclosure with two 920i panel mount indicators. Inside the enclosure, each 920i uses two six-slot expansion boards to accommodate six dual A/D boards and three 24-DIO boards. A single 1 MB memory board is plugged into a slot on the CPU board, and three relay racks hold 36 dual relays to control checkweighing light towers. Each indicator handles 12 cone-shaped scales to which the mesh bags are attached. Each cone-scale is supported on a 10 kg single point load cell and connected to a light tower with five colored lights. Each operator fills two mesh bags simultaneously.
In the morning, a supervisor initializes the system, selecting a product from a database and the names of the operators who will be working on the line. Operators put an empty mesh bag on each scale and the supervisor zeroes all the scales. The blue light signals operators that the scale is in zero range and ready to be filled. The yellow light signals when the weight is at a low range but approaching the desired weight. The white light signals slight over-weight. The red light signals high over-weight. Both the yellow and white lights go on when the desired weight range is reached, but the system has not yet recorded the information in its database. The green light signals when the 920i has read and stored the weight, and notifies the operator to move the tomato-filled bag to the conveyor belt. All lights remain off until a new empty bag is placed on the cone-scale. When the scale recognizes zero, the blue light signals to begin the new filling process.
During the day, supervisors can monitor the process on a PC screen. They can see how many bags each operator has filled, and how many bags were filled over and under the desired range. They also monitor a screen totaling the same information for all 12 operators on the packing line.
At the end of the day, the packing manager connects to the network using an Excel® file with macros that send commands to all five packing line controllers. All data recorded during the day is downloaded to the packing manager’s computer. The manager then generates reports used to pay bonuses and incentives to operators depending on their individual performance.
Gustavo reports, “The 920i provides us with the accuracy of measurement we need for our customers and our employees. We are confident that our product is going out at the correct weight—not underweight and not overweight. It has also allowed us to increase the speed of our production line.”
With the 920i system, Desert Glory is packing 100 percent more than they were before, with the same number of operators. And those very pleased operators finish their workday two hours earlier than before the 920i system was in place. Instead of a daily production of eight metric tons, Desert Glory is now packing 16 metric tons of cherry tomatoes a day. That’s a 100 percent increase thanks to Rice Lake’s 920i controlled system.
Holy tomatoes!
Germany
720™ and 420 Plus™ DC weigh on-board
Oberhonnefeld, Germany — After eight years of selling and servicing weigh indicators for an American scale company in Germany, Heinz Gerd Schneider, salesman, and Horst Reinhard Pilz, service manager, made the decision to start their own business. They founded S+P Wägetechnik GmbH in 1990, selling and servicing weigh indicators, load cells, printers and remote displays to scale manufacturers and integrators. S+P Wägetechnik GmbH has been a Rice Lake distributor for weighing indicators in Germany since 2002.
Not too long after opening their doors, S+P Wägetechnik GmbH received a call from a customer looking for an on-board weighing system for a tip lorry. The impetus for the call was the increasing deposit charges for waste and garbage. With an on-board weighing system the driver has the ability to print a weigh ticket in the cab of the truck, eliminating the expense of driving to a scale and paying to be weighed in order to receive a weight ticket. The on-board weighing systems on the market at the time were approved as Class IV, which has a maximum number of verification scale intervals of 1,000. Heinz and Horst’s goal was to develop a more accurate on-board weighing system approved as Class III, with a maximum number of verification intervals up to 3,000.
Most of these systems can be retro-fitted to vehicles. A printer is a standard component of every system, and Heinz and Horst know Rice Lake’s 720i HMI indicator can provide any function their customers require in the future.
They use the 420 Plus DC version for all applications without level compensation. The 420 Plus indicator provides the basic functions for the application and features a real-time clock; numeric tare entry; ticket print formatting; two serial I/O s for printer, computer or remote display; and digital I/O s for remote tare and print.
Rice Lake implemented custom software in the 520 indicator to compensate the weight according to the level. In applications with level compensation, a four-axis RS-232 sensor sends angle data.
All systems are OIML Class III approved by the Physikalisch-Technische Bundesanstalt (PTB), the national metrology institute in Germany.
Today, S+P Wägetechnik GmbH is the leading manufacturer of Legal-for-Trade on-board weighing systems in Germany and has customers in Belgium, France, Italy, Luxembourg, Netherlands, Austria and Switzerland. They offer a wide range of weighing systems using the 420 Plus, and 520 with special software that allows automatic level (tilt) compensation up to 6 degrees for each axis.
In the future, after getting OIML approval, S+P Wägetechnik GmbH will be using the new Rice Lake 720i DC indicator which has even more functions including multi-interval, alibi storage, programmability, databases, graphic display, external keyboard and more I/Os.
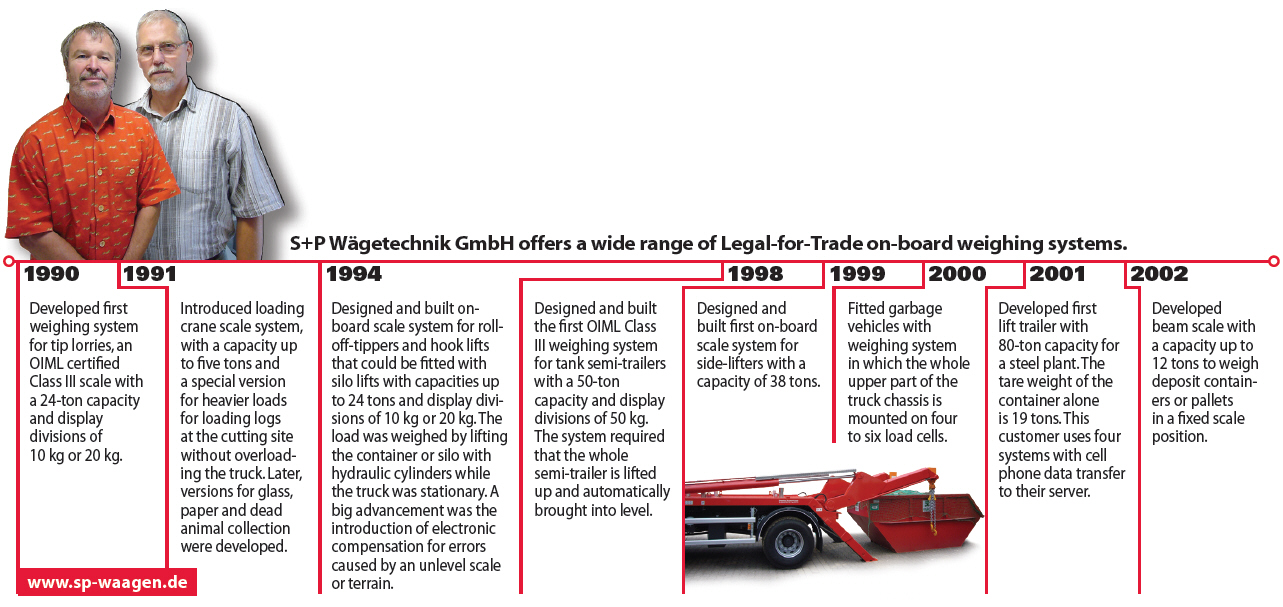
United Kingdom
420 Plus™ batches chemicals
READING, United Kingdom — Applied Weighing International recently installed Rice Lake’s 420 Plus digital weight indicator at Kent-based Monarch Chemicals. Monarch Chemicals is one of the largest and most progressive chemical manufacturers and distributors in the UK, and the blending facility at their Kent site is their latest major investment.
The company decided to switch to the 420 Plus in order to increase their production. The 420 Plus, with its full numeric keypad, allows tare entry directly from the keypad for weighing contents of intermediate bulk containers (IBCs), cylinders and containers, eliminating the need to scroll and toggle weight values. The 420 Plus also drives up to eight 350 ohm load cells, making it the perfect choice for multi-cell applications. It is encased in a tough, all stainless steel IP66/NEMA 4X enclosure that is extremely
durable, even in the harshest environments. In addition, the system features Rice Lake’s three-stage RATTLETRAP® digital filtering that eliminates vibration interference and provides stable, accurate weight data regardless of environment.
Having successfully operated the system at the factory for a number of months, Trevor Goddard, group project manager at Monarch Chemicals, had no hesitation when asked to comment on how the installation is working for them. According to Trevor, “Doing business with Applied Weighing has worked out extremely well for us. The system has helped us more than we could have hoped, and their ongoing service and support has made the whole process run smoothly. Our confidence in Applied Weighing and their system has enabled our production team to manufacture to a higher degree of accuracy and efficiency. This has allowed our company to develop our chemical blending and manufacturing for UK businesses.”
Applied Weighing, which was first established in 1990, provides a complete range of weighing solutions and systems. These are custom built to meet individual customer requirements. Their aim is to provide quality products on short delivery times, backed up with comprehensive technical support. Applied Weighing is an ISO 9001:2000 registered company and is certified for the manufacture of ATEX* compliant products.
Singapore
SURVIVOR® PT up in record time and 920i® holds the spice
Singapore — Singapore is an island country that embraces 63 islands that are actually growing in land area, fed by ongoing land reclamation projects. Earth from Singapore’s own hills and seabed and neighboring countries has enlarged its original 224 square miles to 271 square miles today. Another 38 square miles are planned to be added by 2030.
As further proof of Singapore’s enterprising spirit, last September the country was rated as having the most business-friendly economy in the world by the World Bank. Which makes a fine and fertile base for Goldbell Weigh-System Pte Ltd. Steven Lim opened Goldbell Weigh-Systems in 1993 and has been the Rice Lake distributor in Singapore for more than 10 years.
In 2005, the first truck scale system to be shipped direct from the United States to Singapore was installed by Goldbell at SMA Peakmore Pte Ltd, a local recycling
and trading company dealing in steel and scrap metal, it was a Rice Lake SURVIVOR® PT Series 60 x 10 foot pit type truck scale system, 920i, iQUBE® 8-channel Smart Junction Box with two fiber optic to serial converters.
The total excavation, construction, installation and instrumentation took two months to complete. In Singapore’s tropical rainforest climate, where the average humidity is 90 percent in the morning and 60 percent in the afternoon, the concrete deck took only seven days to cure.
How did they accomplish that record drying time? We asked Richard Tan. “We modified the soffit of the slab a bit. Instead of using corrugated sheets, we used a material called Condeck™ which is a system that interlocks each individual sheet together forming a solid working platform. The ribbed shape stiffens the whole platform where ordinary corrugated GI sheets would not. We used high-strength quick-setting Grade 45 concrete that gains sufficient strength within seven days that ordinary Grade 30 would not be able to achieve. Before loading the bridge, we did a field test on the density of the concrete by means of a rebound hammer test. Theoretical calculations over strength gain are 75 percent at seven days, which is 22.5N/mm2 for normal Grade 30, and 33.7N/mm2 for a Grade 45. The actual results achieved averaged 39 to 42N/mm2.” Seven days later, CMA Peakmore began using their 80-ton capacity concrete deck weighbridge and has never had a minute of downtime.
Another happy customer of Goldbell is the Lee Kwang Kee Seafood Restaurants that have sprouted up all over Singapore’s islands. Their system is made up of stainless steel platform scales controlled by 920i s with custom iRite® software.
The system has helped to monitor certain key ingredients that the chefs use in preparing the unique seafood dishes. The system also helps balance the outflow of ingredients against collected revenue, as well as keeping tabs on each chef’s skills.
The operator, or chef, places an empty container on the scale and presses the tare key, then adds the secret ingredients. When the weight on the scale exceeds the minimum threshold, the weight is recorded. When the container is removed from the scale, the last stable weight reading, time and date are recorded in the database.
It all sounds a bit clinical for the art of preparing seafood delicacies, but Lee Kwang Kee Seafoods’ owner considers the information critical to establishing excellent quality while ensuring the highest return on investment.
Not too much spice, please!
Ukraine
920® controls big blast furnace
Zaporizhstal, Ukraine — Ukraine is located in the southeastern part of Central Europe where it is bordered by Belarus and Russia to the north, and the Black Sea and Romania to the south. One of Ukraine’s 24 administrative regions is the Zaporizhzhya region located in the southeast of Ukraine.
There are more than 160 large industrial enterprises in the region. And Zaporizhstal Integrated Iron & Steel Works JSC is one of the largest. Construction at Zaporizhstal, commonly called “The Works,” began in 1931 and was designed to become the largest enterprise in Europe at that time, with an annual capacity of 1,224,000 tons of pig iron and 1,430,000 tons of premium quality steel.
Today, The Works produces high quality hot-rolled and cold-rolled carbon, low-alloy, alloy and stainless steel products from 0.5 to 8.0 mm thick. Main consumers of The Works’ products are welded tube producers, automotive, machine-building, transport engineering industries and producers of domestic appliances.
To improve the quality of their steel, a unique patented technology was introduced using a mixture of argon and oxygen in the open-hearth furnace shop. The quality and competitive strength of Zaporizhstal’s enterprise products (alloy sheets and stainless steel, dipped tinplate in rolls, cold-formed profiles and metal-base laminate) are recognized and renowned worldwide.
Recently, The Works updated the batching and loading systems of blast-furnace No. 5 where temperatures reach 800 degrees Celsius. The system must withstand incessant operation with the most stringent accuracy. The Works uses Rice Lake components: high temperature and protected RL9000TWM load cells, EL146 load cell cables, iQUBE® and 920i indicators.
Paresh Oza, Rice Lake’s director of international field sales, reports that projecting, mounting and starting the system was performed by DKL Ltd. and Trest SZMA, Ukraine. All software was designed and applied by DKL Ltd.
Director Igor Belikov of Trest SZMA recalls, “It was a pleasure working with the staff at DKL to complete this successful installation. We have high regards for DKL’s capabilities and knowledge about Rice Lake’s superior quality products.”
The loading system has two loading sides to the blast-furnace with six bins with capacities from five to 25 tons of agglomerate, coke, pellets, limestone and other agents in each. These materials are supplied by conveyor, loaded into skips and delivered to the blast-furnace. For redundancy, two RL9000TWM load cells are used on each of the three bins. Each scale circuit is connected to separate iQUBEs.
Data is transmitted from the iQUBEs through RS-485 a distance of 500 to 700 meters to 920i indicators installed at the center of blast-furnace loading control. The dozen 920i s are connected to PCs via Ethernet. The process is controlled both via computer with the graphic information output, as well as 920is.
According to Alexey Murashov, a director of DKL Ltd., it was very interesting work. “This successful project will give us an excellent reference to similar installations in other major steel plants in the Ukraine.”
Subscribe to Rice Lake Magazine
Sign in or create a Rice Lake website account to request a Rice Lake Magazine filled with application stories like this one be sent to you.
Account Sign In Create an Account